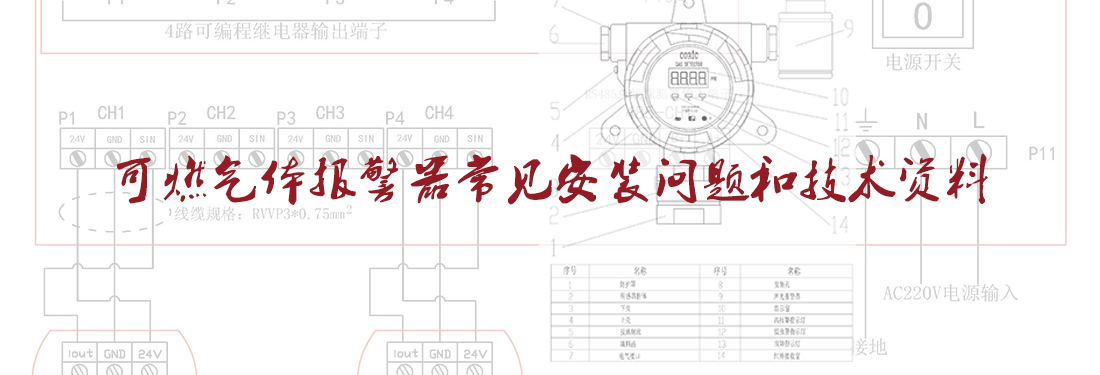
危险化学品企业的有毒有害、易燃易爆气体检测报警系统,在探测到装置设施管道等可燃、有毒气体泄漏时,将泄漏信息传递至控制中心,并以声/光的方式提醒、告知现场人员,有关人员将及时做出必要的人工干预及保护性响应,以避免生产安全事故的发生。
近来,应急管理部明查暗访组、中国化学品安全协会专家每到危险化学品生产、储存企业进行安全检查、诊断,几乎都能查出企业在有毒有害、易燃易爆气体检测报警方面存在若干问题。许多企业没有按照《石油化工可燃气体和有毒气体检测报警设计规范》(GB 50493-2009)和《工作场所有毒气体检测报警装置设置规范》(GBZ/T 233-2009)的要求进行可燃、有毒气体检测报警装置的设置和管理。
在生产或使用可燃气体、有毒气体的工艺装置和储运设施的区域内,有些企业没有设置相应的可燃、有毒气体检测报警装置,这将不能有效预防火灾、爆炸和人员中毒事故的发生。在可燃气体与有毒气体同时存在的场所,有的企业只是设置了可燃气体检测报警装置,但未设置有毒气体检测报警装置,这将不能预防中毒事故发生。有一家企业,在其反应器设备与管道连接大法兰处发生过两次可燃气体泄漏、着火,但该企业仍未按《石油化工可燃气体和有毒气体检测报警设计规范》(GB 50493-2019)第4.1.2条的要求,在法兰处设置可燃气体检测报警装置。
有些企业虽然在生产或使用可燃气体及有毒气体的工艺装置和储运设施的区域内设置了可燃、有毒气体检测报警装置,但存在着不同类型的设置缺陷。
(1)未设置就地声光报警;
(2)报警控制器未设置UPS电源,或者报警控制器UPS电源回路没有供电;
(3)不符合防爆要求:有的是防爆区域的报警控制器为非防爆,有的是气体检测器与报警灯之间防爆接线盒防爆等级低于工程防爆要求;
(4)安装高度或偏高或偏低,不符合《石油化工可燃气体和有毒气体检测报警设计规范》(GB 50493-2009)第6.1条的要求;
(5)通讯、提醒功能存在问题:有的存在主线通讯故障,有的泄漏报警信号未发送至有操作人员常驻的控制室进行报警,还有的未在控制室设置可燃、有毒气体闪烁报警灯;
(6)可燃气体检测报警系统与DCS控制系统使用同一组控制器;
(7)无储存记忆功能;
(8)报警仪未进行固定。
(9)报警器安装了,但是没有通电,应付检查,就是一个摆设;
(10)报警器维护不当,导致传感器口堵死或者外观腐蚀严重;
(11)报警装置布置没有实现可视化;没有按时检定/校准检测报警装置;生产、技术人员对报警阈值及可允许浓度不了解,对报警后应该采取的应急处置措施不清楚;
(12)巡检工判断有毒气体是否泄漏的首选措施居然是靠鼻子闻;
(13)操作人员去存在可燃、有毒气体泄漏可能的区域巡检时,未随身携带便携式可燃、有毒气体检测报警仪;
(14)身在现场的人员不能第一时间接到现场固定式可燃、有毒检测报警装置的预警;便携式报警仪测得的数据没有即时记录,独立于系统监管之外;报警发生时,不能实现全局立体互联,成为信息孤岛。
(15)没有按照《石油化工可燃气体和有毒气体检测报警设计规范》(GB 50493-2009)和《工作场所有毒气体检测报警装置设置规范》标准要求设置报警值大小,至少设置两级报警值。
(16)没有安排专职人员对报警器进行管理维护,现场不知道报警器安装在什么地方,一问三不知;
(17)安装的报警器没有联动或者控制器没有设置联动,比如联动现场排风扇以及切断阀等外部设备;
(18)报警器检测气体没有明显的标识,不知道检测什么气体;
(19)报警器安装时间很长,有些都是五六年了,传感器已经无法工作,还在现场安装,基本上是摆设;
(20)报警器长时间不校准,导致数据漂移,检测灵敏度下降;